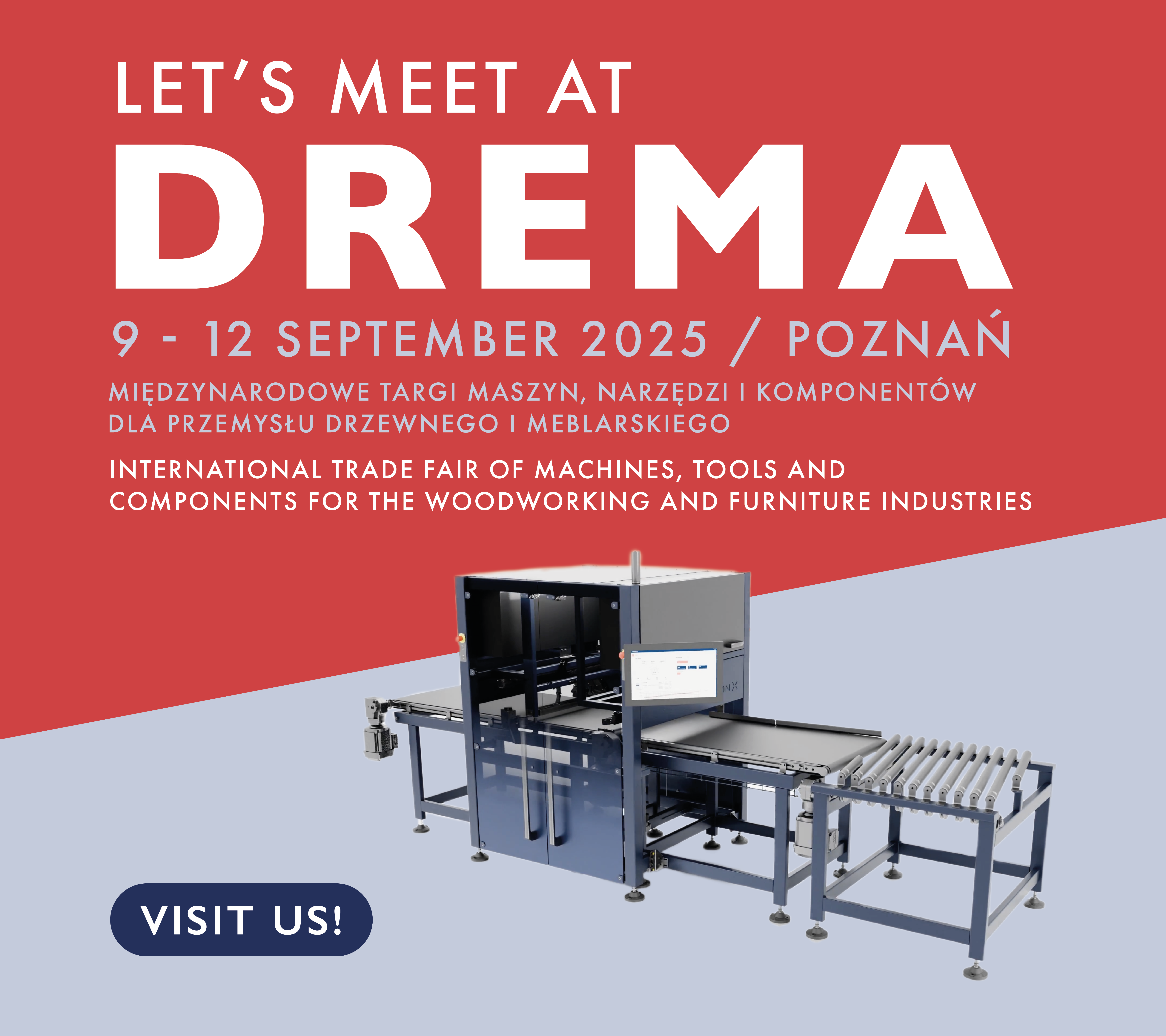
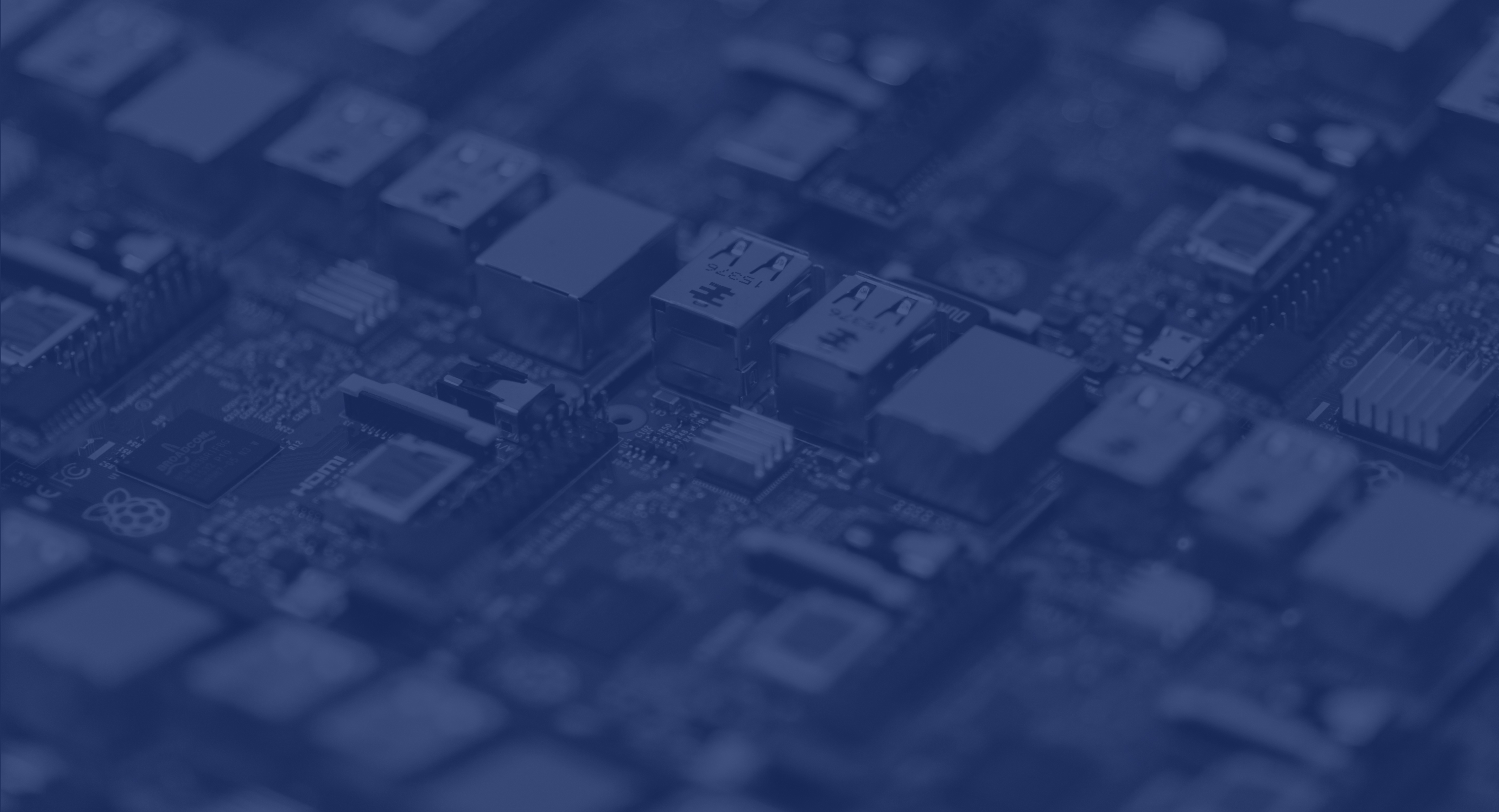
25/6/2025
Electronics
How Do We Test PCBA Boards? PCBA Tester and Electronics Quality Control
Discover how our automatic PCBA tester works – a system that detects missing components, incorrect polarity, and soldering issues in just a few seconds. Camera precision, intelligent image analysis, and zero randomness. See how we can improve your quality control.
Czytaj dalej
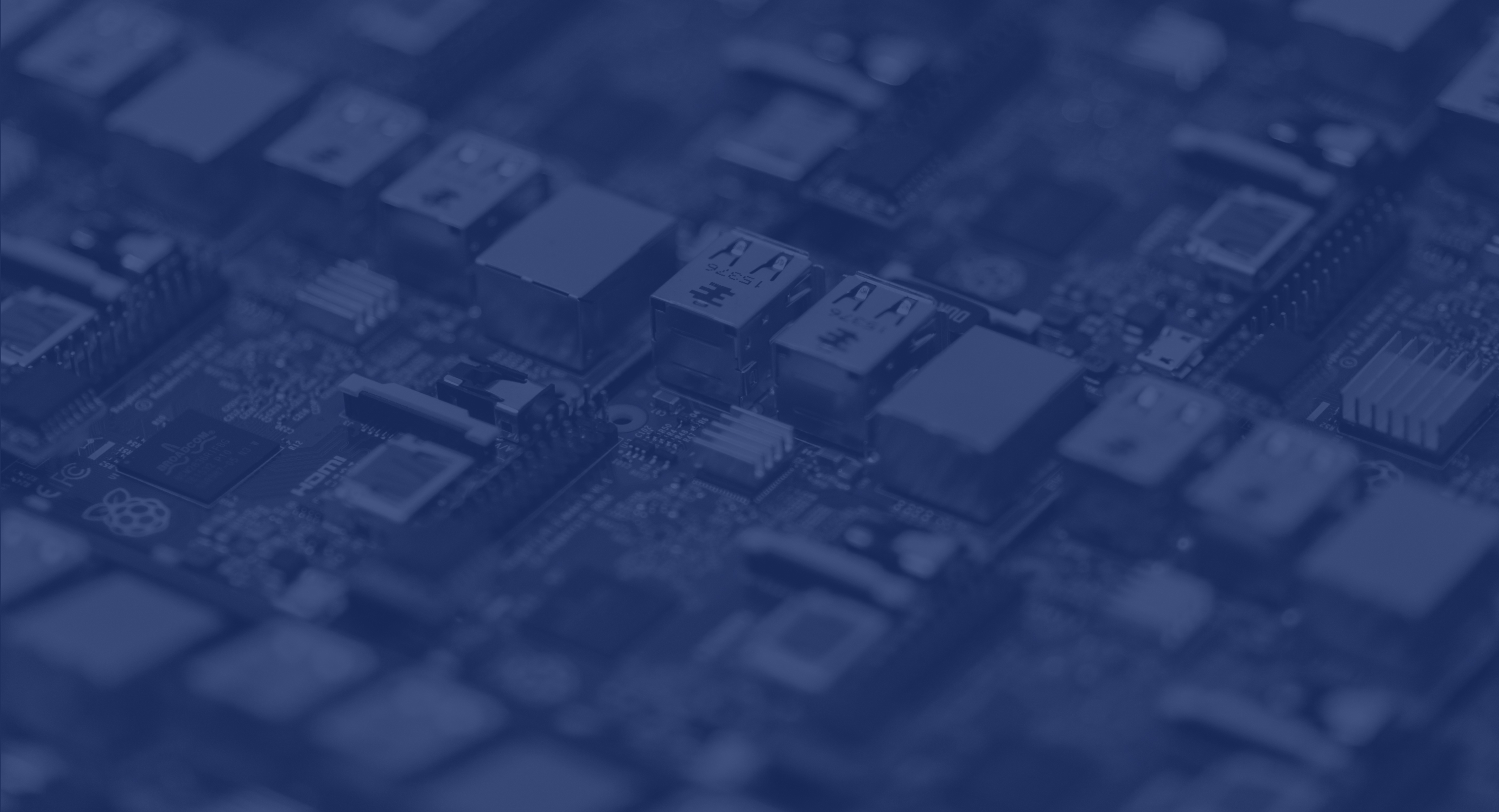
25/6/25
Electronics
How Do We Test PCBA Boards? PCBA Tester and Electronics Quality Control
At VisionX, we specialize in vision systems for quality control. One of the key elements of our offering is the PCBA tester – a system for automatic inspection of printed circuit boards after assembly. The tester checks the correct placement, soldering, and polarity of all components.
It detects missing parts, incorrect markings, and hard-to-spot errors, such as a reversed capacitor or a missing plug in a connector.
How Do We Test PCBA Boards?
The testing process is fully automated and highly repeatable. At the heart of the system is an industrial camera mounted on a movable drive that moves over the PCBA board secured in a custom fixture. This motion allows inspection of every section of the board with very high accuracy, without the need for manual handling.
1. Fixture Tailored to Each PCBA Board
Each PCBA board can have different dimensions, component layouts, or reference points – that’s why we design a dedicated fixture. It holds the board securely in place and ensures precise, repeatable testing with no shifts or positioning errors. It is designed to prevent incorrect placement of the board.
2. Camera Moves Over the Board
The camera moves on its drive and inspects all the elements on the board by taking sequential images. Depending on the number of components, this takes about 6 seconds. At each position, a high-resolution photo is taken and then analyzed by software.
For example: with 300 components on a single-sided board of size 20 cm x 15 cm, testing takes approximately 6 seconds – including tray movement in, camera travel with inspection, and tray movement out.
3. Darkfield Illumination
We use darkfield lighting for inspection – this means components are illuminated from the side, and the camera captures the shadow cast by each element. If there is no shadow, it means the component is missing – a simple but highly effective principle.
This allows us to automatically detect:
- Missing components
- Incorrect orientation (e.g., reversed electrolytic capacitor)
Additionally: - Polarity issues with diodes, LEDs, ICs
- Improper solder presence or cold joints
4. Vision Algorithms
Image analysis is based on methods such as image thresholding, pixel counting, and pattern matching. This allows us to detect not only the physical presence of components but also the correctness of assembly and quality of workmanship. For more complex components – e.g., multi-layer parts – we apply specialized algorithms tailored to the component type.
5. Logging Results and Statistical Analysis
Each inspected board has its results saved. The system can be integrated with the client’s database or MES system – enabling:
- Tracking test history for each batch
- Generating reports on defects and rejections
- Analyzing production trends and identifying the most common issues
Why Is This Solution the Best?
Automated vision inspection with a camera on a drive is a precise, repeatable, and flexible method of PCBA testing, far superior to manual inspection. A system independent of the operator ensures a consistent level of quality, eliminating human error and fatigue.
Fewer complaints, better quality control, and more reliable production.
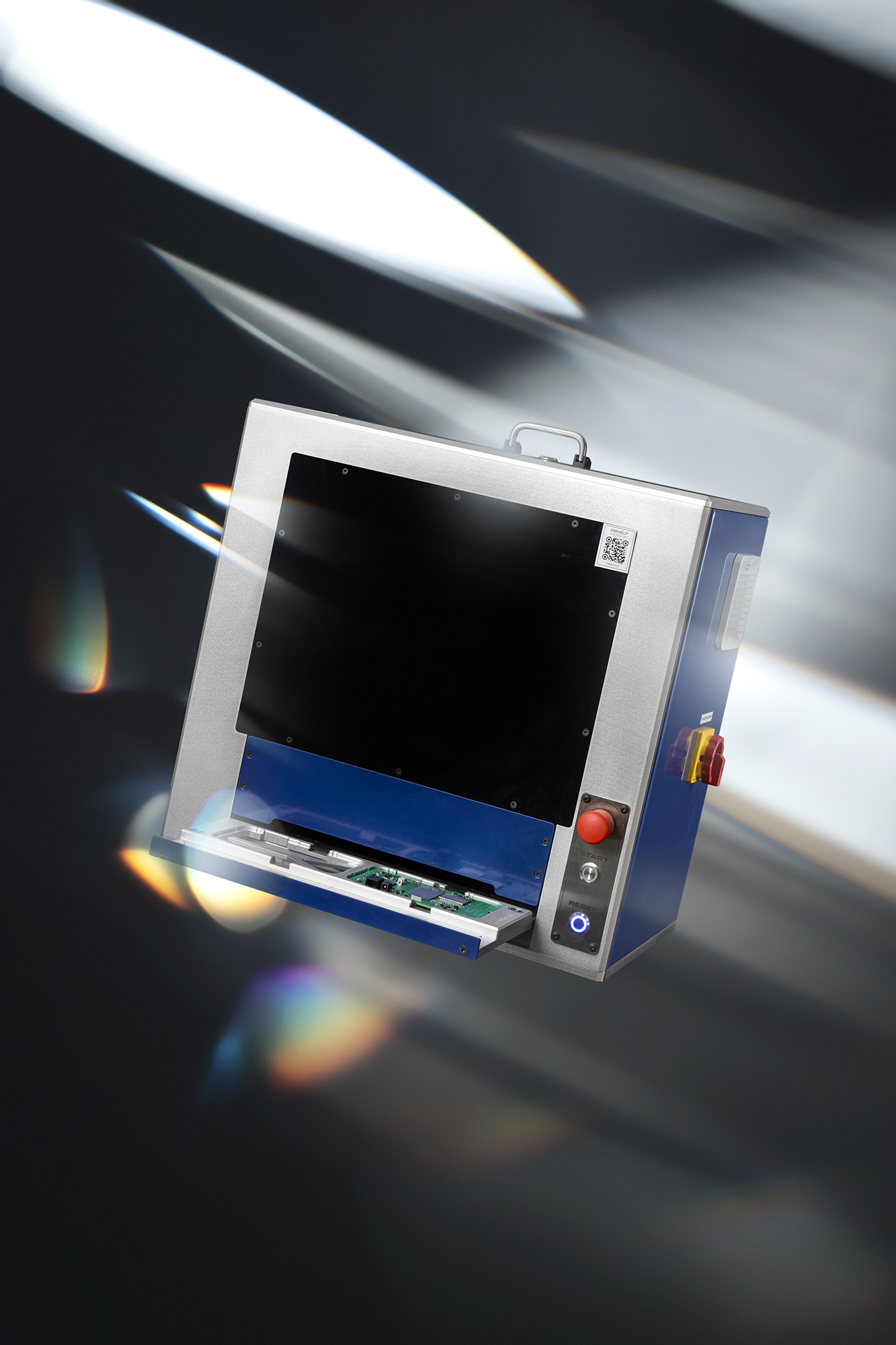
See other articles
Contact
So what, shall we begin? Call or email us!
Phone
+48 724 727 444E-mail
INFO@VISIONX.COM.PLRegistration data
Name
VisionX Sp. z o.o.
Address
Oliwska 21/23, 80-563, Gdańsk
NIP
5833441185
REGON
520574098
Use the form. We will reply within 24 hours!
Thank you! Your submission has been received!
Oops! Something went wrong while submitting the form.