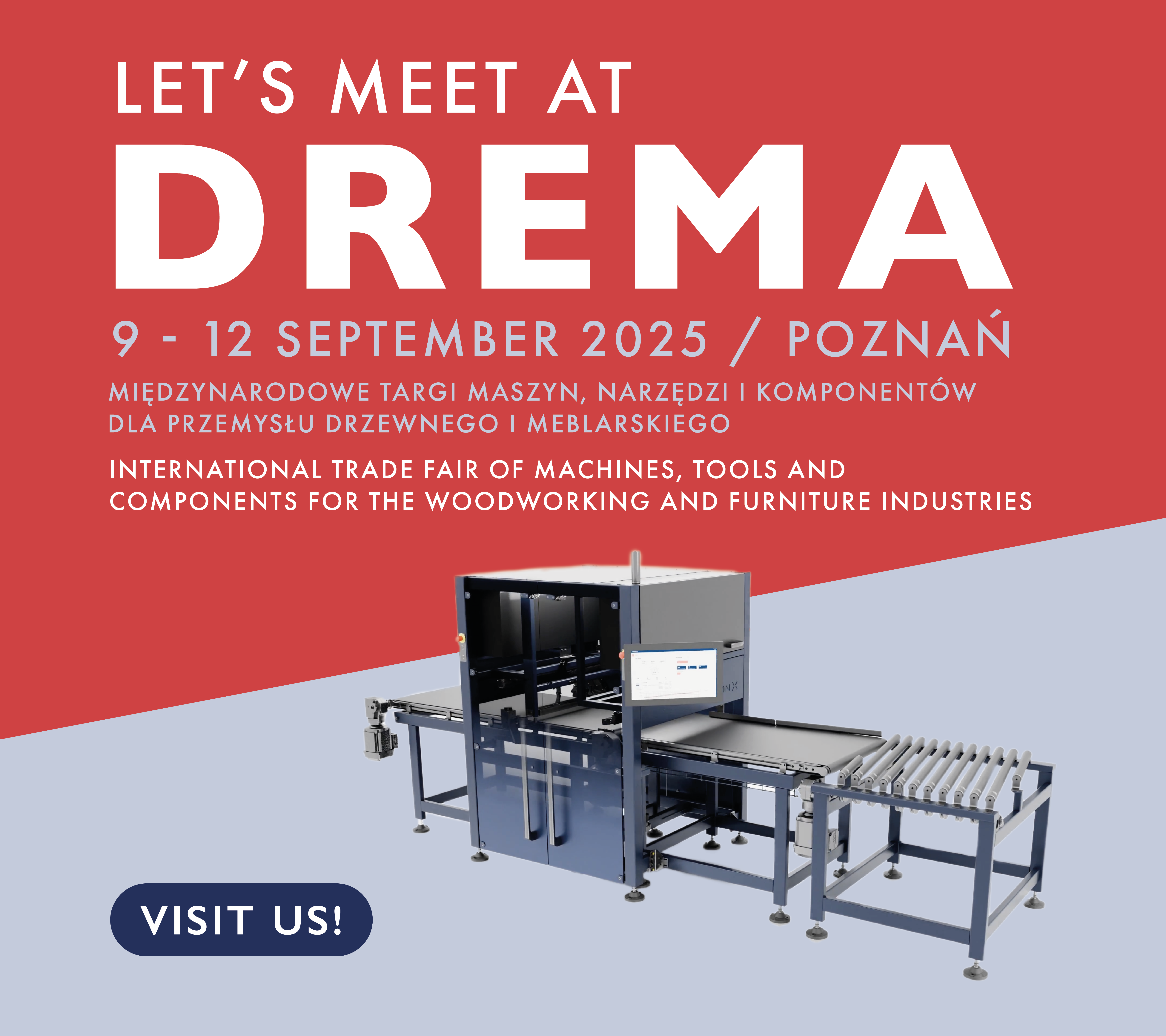
.avif)
10/8/2025
Window Profiles
Primer control system
How can you detect invisible defects, improve quality, and increase workplace safety? In this case study, we show how automatic primer inspection significantly improved profile production – without rebuilding the line and without compromises!
Czytaj dalej
.avif)
27/12/24
Window Profiles
Primer control system
Primer control system
This is an automated vision system designed to inspect the primer layer applied before bonding or painting production components. Its purpose is to detect missing areas, excess application, or uneven distribution of primer, ensuring high quality and process consistency. By using cameras and UV light sources, the system operates quickly, accurately, and without posing any risk to operators.
The Challenge
A manufacturer of door and window profiles was looking for an effective way to control the primer layer applied before gluing and painting. The existing inspection process relied on:
- Manual checks using UV-A light
- A high risk of human error
- Significant exposure of workers to radiation
- Undetectable defects such as partial coverage or streaks
These issues led to production losses, customer complaints, and health risks for operators.
.avif)
The Solution
We implemented a fully automated vision system for primer inspection, specifically designed for high-throughput production lines.
Key features of the solution include:
- 360° inspection of profiles at speeds up to 26 m/min
- Compatibility with profiles of various geometries, sizes, and colors
- Use of UV light sources to detect primer surface properties through fluorescence
- Entire inspection process enclosed in a sealed housing to eliminate operator exposure to UV radiation
- Automatic estimation of coating weight (g/mm²)
- Detection of defects such as:
- Insufficient or excessive primer
- Uneven distribution
- Local imperfections (e.g., splashes)
- Error alerts for the operator (visual and audible)
- Image capture for reporting and verification
- Intuitive interface with the ability to define custom profile shapes
- Seamless integration without modifications to the production line's mechanical structure
The system was designed with safety, precision, and scalability in mind.

Results
Thanks to the implementation of the system, the client achieved:
- Over 90% reduction in defects related to primer application
- Complete elimination of personnel exposure to UV-A radiation
- Consistent coating quality regardless of operator changes
- Return on investment within 3–6 months
- The ability to report and track quality data
The automation of inspection resulted in tangible cost savings and increased satisfaction among end customers.
Summary
Our primer inspection system combines vision technology, safety, and performance. The client gained process repeatability, fast error detection, and real savings – all without any modification to the production line.
The implementation demonstrated how modern vision inspection can completely transform the approach to quality and efficiency in industrial production. A client who previously struggled with hard-to-detect errors, customer complaints, and hazardous inspection methods (such as UV-A exposure) now benefits from a solution that:
- Eliminates risks to personnel
- Operates fully automatically and continuously
- Enables immediate issue identification and prevention
- Delivers concrete data and images ready for quality analysis or audits
This system not only solves a real problem, but also provides added value – through improved process consistency, reduced material waste, enhanced reporting, and clearly increased customer satisfaction.
It’s a strong example that quality control automation isn’t a cost – it’s an investment in reliability.
See other articles
Contact
So what, shall we begin? Call or email us!
Phone
+48 724 727 444E-mail
INFO@VISIONX.COM.PLRegistration data
Name
VisionX Sp. z o.o.
Address
Oliwska 21/23, 80-563, Gdańsk
NIP
5833441185
REGON
520574098
Use the form. We will reply within 24 hours!
Thank you! Your submission has been received!
Oops! Something went wrong while submitting the form.