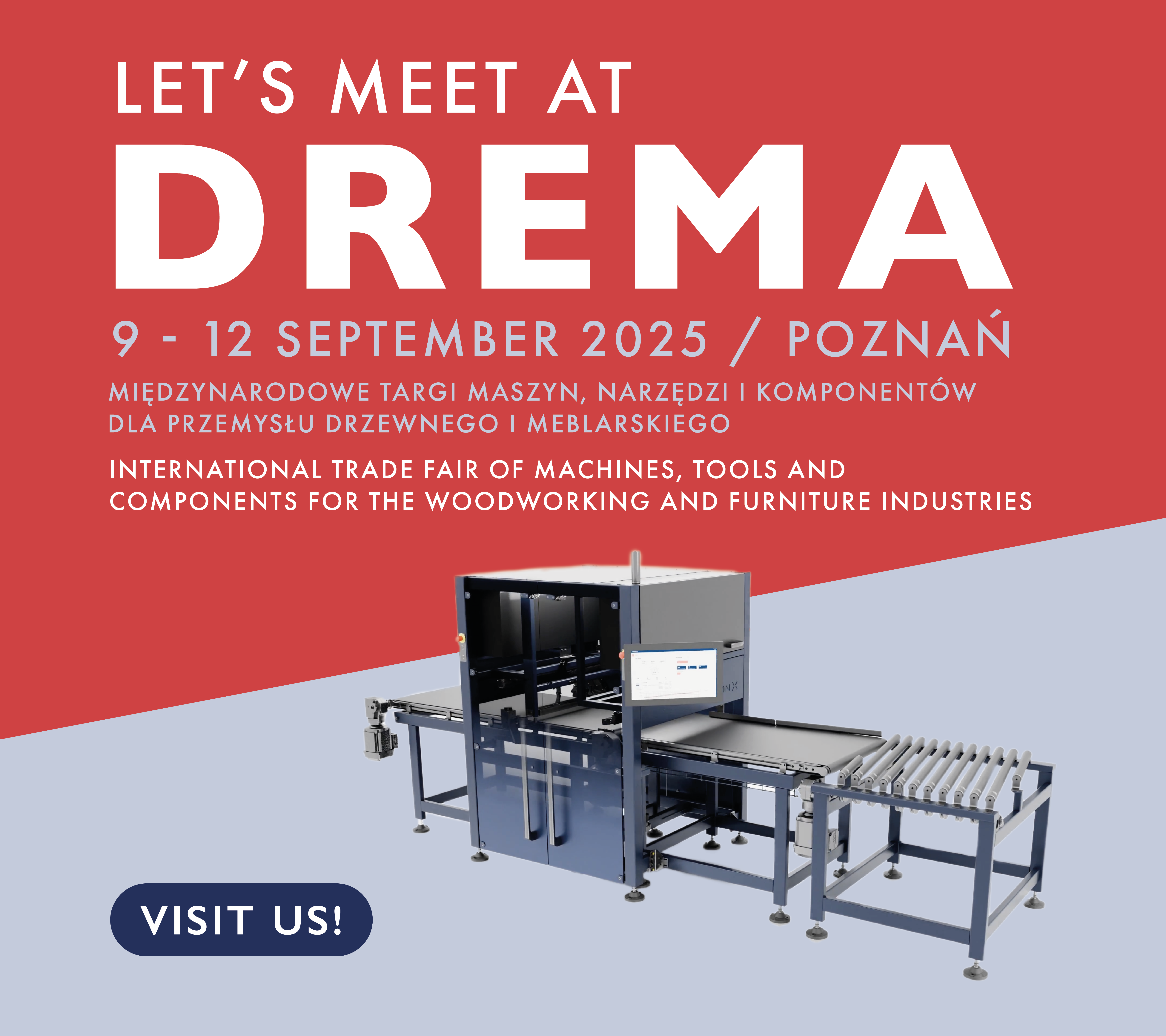
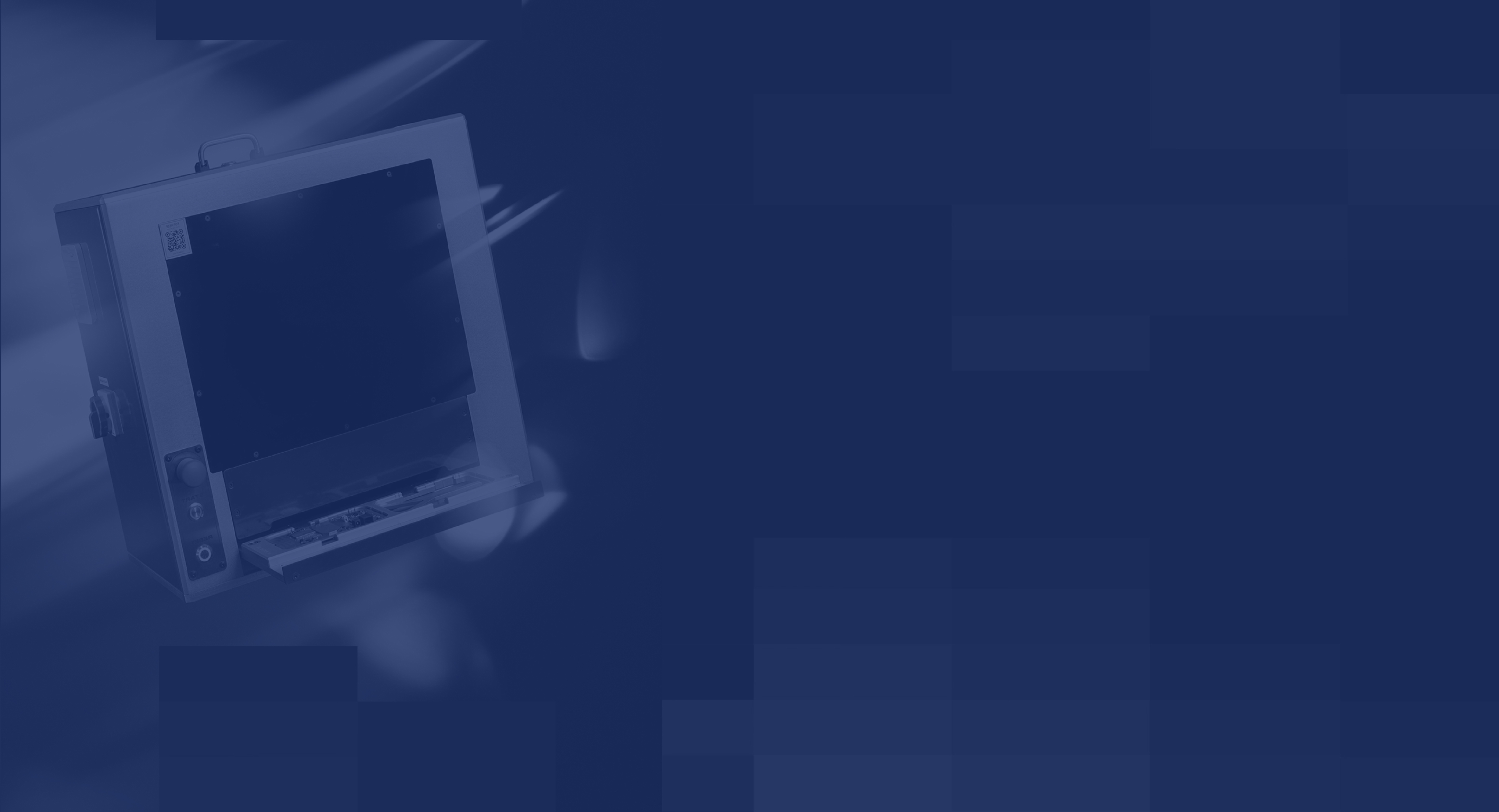
10/8/2025
Automotive
Is your quality control sufficient?
Did you know that up to 30% of production costs can result from detecting and fixing quality defects? These are significant losses that can be reduced through effective quality control. A modern approach to inspection not only lowers costs but also increases efficiency, improves safety, and builds customer trust.
Czytaj dalej
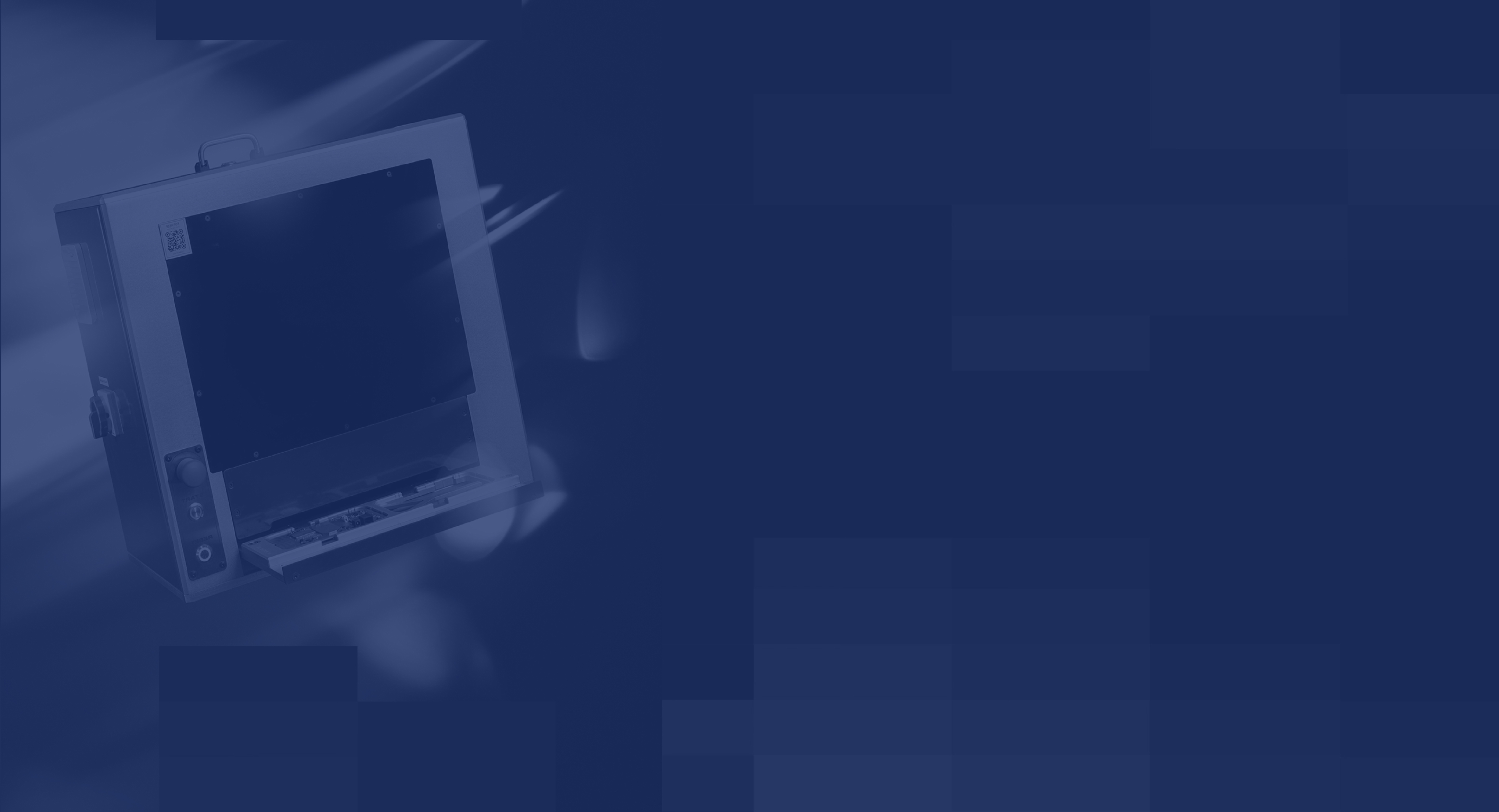
27/5/25
Automotive
Is your quality control sufficient?
Is your quality control good enough?
Did you know that up to 30% of production costs can result from detecting and fixing quality defects?
These are huge losses that can be reduced through effective quality control. A modern approach to inspection
not only lowers costs but also increases efficiency, improves safety, and builds customer trust.
At the end, we will present the PCBA Tester – an advanced device for automatic PCB inspection.
Discover its features and find out how it can help optimize your production!
The most common quality control mistakes – avoid them!
- Relying solely on manual inspection – high risk of overlooking defects.
- Lack of clearly defined standards – leads to chaos and ineffective procedures.
- Inadequate employee training – systems don’t work without skilled personnel.
- No data integration – difficulty in analysis and fast decision-making.
- Incorrect measurement parameters – lack of precision in quality assessment.
Long-term benefits for your company with our vision system:
✔ Reduced production costs – eliminate defects during production.
✔ Higher customer satisfaction – high quality builds loyalty and trust.
✔ Compliance with regulations – meet safety and quality standards.
✔ Process optimization – improved efficiency and higher OEE rates.
✔ Better raw material control – minimize material waste.
Best practices in quality control
- Regular calibration and modernization of measuring systems.
- Implementation of traceability – tracking quality at every production stage.
- Procedure standardization – clear guidelines and instructions for the team.
- Continuous training – enhancing employee competencies.
- Real-time monitoring – using IoT and MES systems.
- Continuous improvement – analyzing quality data and implementing enhancements.
- Cross-department collaboration – exchanging information between production, maintenance, and quality control teams.
PCBA Tester – Our solution for quality control
Our PCBA Tester is an advanced vision inspection device designed for precise, automated inspection of PCBs,
minimizing production errors and optimizing the quality control process.
How does it work?
- Fixture with sockets – the tester can handle one or two PCBs at once, depending on their size. For larger boards,
inspection is done individually. In standard testers, we do not use more than two PCBs at the same time,
but the system can be customized based on client requirements. - Automatic inspection – once the PCBs are inserted and “Start” is pressed, scanning begins.
- Movable camera – moves over the PCB in an efficiency-optimized manner, enabling fast analysis of all components.
- Inspection screen – the operator sees the PCB status in real time, including damaged components and their exact location.
- Quality statistics – the system tracks and records production success rates.
- Safety – if the operator accidentally puts a hand into the device, a safety relay alarm is triggered and the system requires a reset button press.
- Support for various PCBs – the tester can analyze both small boards with a large number of components
(e.g. 1000 elements) and large boards with fewer components. Physical size determines whether boards are inspected singly or in pairs. - Integration with external systems – supports connection to external drives and MES-class systems, enabling detailed defect history analysis.
Why choose it?
✔ Objectivity – the system eliminates the “human factor” through precisely defined evaluation criteria.
✔ Speed – verification time depends on PCB size and component count. Small boards can be analyzed in about
5–8 seconds; medium and large ones typically take 8–10 seconds.
✔ Safety – reduces operator eye strain through automated inspection.
✔ Communication – full control over data and flexible archiving options.
✔ Cost-effectiveness – lowers costs by replacing manual inspection with automation.
Additional features:
- Double-sided inspection – the system analyzes both sides of the board.
- Minimization of false rejects – advanced verification ensures maximum precision, reducing the risk of incorrect labeling to an absolute minimum.
- THT and SMD component verification – detects presence, damage, and polarity.
- Remote access – remote connection to the application available.
- Optional solder joint analysis – additional function to check soldering accuracy.
- Quick implementation – complete system launch support.
PCBA Tester is an innovative solution that significantly improves production quality, minimizes the risk of returns, and increases inspection efficiency.
https://www.linkedin.com/company/13996756/admin/products/visionxpl-vision-systems-pcba-tester/
See other articles
Contact
So what, shall we begin? Call or email us!
Phone
+48 724 727 444E-mail
INFO@VISIONX.COM.PLRegistration data
Name
VisionX Sp. z o.o.
Address
Oliwska 21/23, 80-563, Gdańsk
NIP
5833441185
REGON
520574098
Use the form. We will reply within 24 hours!
Thank you! Your submission has been received!
Oops! Something went wrong while submitting the form.